Mastering Welding WPS Criteria: Ideal Practices and Techniques for High Quality Welds
In the world of welding, mastering Welding Procedure Spec (WPS) requirements is an important part that straight affects the high quality and integrity of welds. Complying with these standards guarantees consistency and reliability in welding results. However, attaining excellence in welds surpasses just comprehending the criteria; it includes carrying out ideal practices and strategies that raise the craft to a degree of accuracy and skill that distinguishes the average from the extraordinary. As we navigate with the details of welding WPS criteria, revealing vital understandings and strategies for accomplishing top-tier welds will certainly be paramount for welders seeking to master their craft and generate welds that stand the test of time.
Comprehending Welding WPS Standards

Recognizing WPS criteria is essential for welders, inspectors, and designers entailed in welding operations. By adhering to WPS guidelines, welders can generate welds that fulfill the called for mechanical residential or commercial properties and structural integrity. Inspectors depend on WPS paperwork to confirm that welding treatments are being adhered to correctly and that the resulting welds are of excellent quality. Designers use WPS requirements to make welding treatments that guarantee the sturdiness and reliability of bonded frameworks.
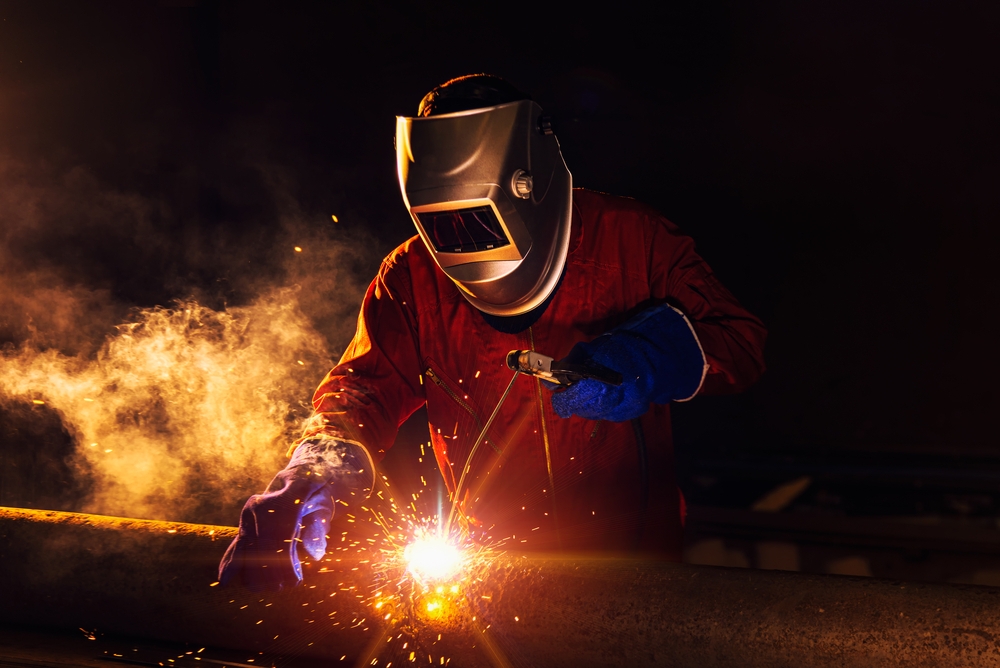

Vital Devices for Top Quality Welds
Understanding welding WPS standards is crucial for welders to successfully use the vital tools needed for creating top quality welds. One of one of the most crucial devices for top quality welds is a welding machine. The type of welding machine needed relies on the welding process being made use of, such as MIG, TIG, or stick welding. Welding safety helmets are likewise vital to protect the welder's eyes and face from sparks, heat, and UV radiation. In addition, welding gloves constructed from long lasting and heat-resistant materials secure the hands from injuries and burns. Magnets and clamps aid hold the work surfaces with each other securely throughout the welding procedure, making certain precise and precise welds. Cable brushes and cracking hammers are vital for cleaning check the weld joint prior to and after welding to remove any kind of impurities that can influence the high quality of the weld. Lastly, a gauging tape and angle mill work tools for guaranteeing proper positioning and preparing the work surfaces for welding.
Key Methods for Welding Success
To achieve welding success, one should understand the vital methods crucial for creating high-quality welds. Maintaining a steady welding and a steady hand position throughout the procedure is crucial to attaining precision and uniformity in the welds. By understanding these vital strategies, welders can elevate the top quality of their job and attain welding success.
Ensuring Compliance With WPS Requirements

In addition, welders ought to undergo training to familiarize themselves with the WPS requirements pertinent to their work. Normal audits and inspections ought to be performed to verify that welding activities align with the suggested WPS guidelines. Additionally, preserving comprehensive records of welding specifications, devices calibration, and assessment results is critical for demonstrating conformity with WPS criteria - welding WPS. By diligently sticking to WPS criteria, welders can guarantee that their work satisfies the required quality levels and adds to the total success of the welding project.
Troubleshooting Common Welding Issues
When confronted with common welding problems, identifying the root cause is vital for reliable troubleshooting. One common problem is the presence of porosity in welds, often triggered by impurities such as corrosion, oil, or wetness. To resolve this, making sure proper cleansing of the base steel before welding and using the right protecting gas can considerably reduce porosity. One more concern regularly encountered is absence of combination, where the weld stops working to effectively bond with the base material. This can stem from inadequate heat input or incorrect welding method. Adjusting specifications such as voltage, cable feed speed, or travel speed can assist enhance fusion. Additionally, distortion, breaking, and spatter are usual welding difficulties that can be reduced with proper joint prep work, regular warm control, and choosing the ideal welding consumables. By extensively understanding these usual welding problems and their source, welders can effectively fix issues and accomplish top quality welds.
Final Thought
In final thought, understanding welding WPS criteria calls for a thorough understanding of the guidelines, using vital devices, and applying vital strategies for effective welds. Making sure compliance with WPS criteria is critical for creating high quality welds and staying clear of typical welding concerns. By following finest techniques and methods, welders can achieve dependable and constant cause their welding jobs.
In the world of welding, mastering Welding Treatment Specification (WPS) criteria is an essential element that straight affects the high quality and stability of welds.When delving into the realm of welding methods, a critical facet to comprehend is the relevance and details of Welding Treatment Requirements (WPS) criteria. WPS criteria supply a thorough standard for welding operations, making sure uniformity, top quality, and security webpage in the welding process. The type of welding equipment needed depends on the welding procedure being utilized, such as MIG, TIG, or stick welding.Accomplishing welding success with the proficiency of essential methods necessitates a thorough understanding and adherence to Welding Procedure Spec (WPS) criteria.